Medical X-ray films play a crucial role in healthcare, providing detailed images of bones, tissues, and organs for diagnostic purposes. The quality of these films directly affects the accuracy of medical diagnoses, making the manufacturing process critical to ensuring their reliability. This blog will walk you through the step-by-step process of manufacturing medical X-ray films and how quality control is maintained throughout the process.
Table of Contents
Introduction: A Brief Overview
Medical X-ray films are designed to capture and retain detailed images produced by X-ray equipment. Their manufacturing process is rigorous, with an emphasis on cleanliness, precision, and quality control, ensuring accurate and clear images.
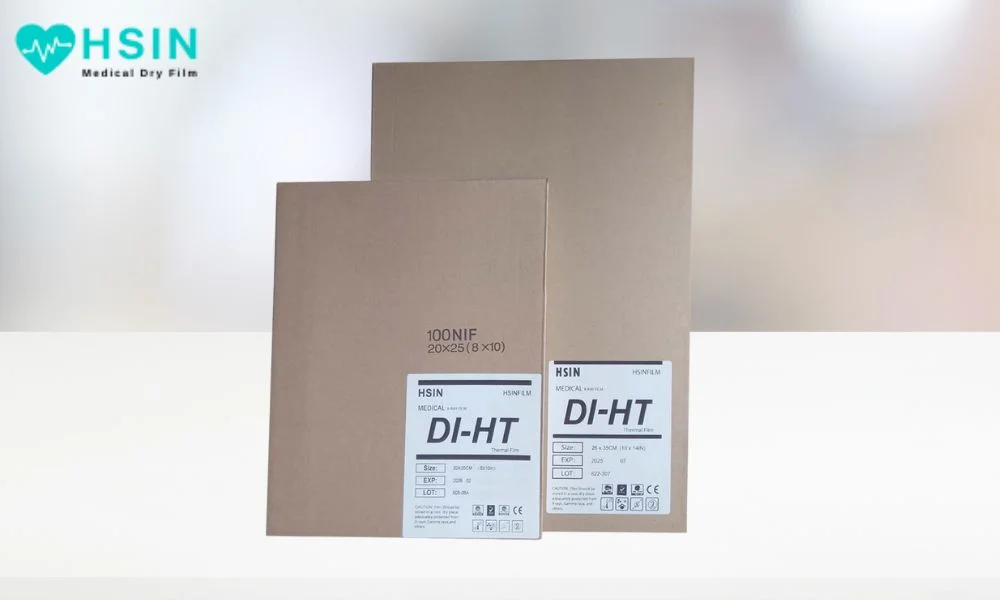
What Are Medical X-Ray Films?
Medical X-ray films are a special type of photographic film used to capture X-ray images. They are designed to be sensitive to the radiation produced by X-ray machines, creating images that help doctors diagnose fractures, diseases, or abnormalities within the body. These films are made using a combination of chemical coatings and materials that respond to X-rays by creating an image after processing.
Importance of High-Quality X-Ray Films
The quality of X-ray films is vital in the healthcare industry. Poor-quality films can result in unclear or inaccurate images, which can lead to misdiagnosis or the need for repeat imaging. High-quality films, on the other hand, provide sharp, detailed images, allowing healthcare professionals to make informed decisions about patient care.
Ensuring the quality of X-ray films begins with the manufacturing process. Every step, from selecting raw materials to packaging, plays a role in producing reliable, high-performing films.
Composition of X-ray Film
X-ray film consists of multiple layers, each with a specific purpose that contributes to the film’s ability to capture and display diagnostic images. The primary components of X-ray film are the emulsion layer and the base layer, both of which are made from specific materials that influence the film’s sensitivity, contrast, and durability.
1. Base Layer
The base layer, or substrate, is the foundation of X-ray film and provides structural support. Historically, X-ray films used a glass or cellulose nitrate base, but modern X-ray films are generally made with polyester due to its superior characteristics.
Materials in the Base Layer:
- Polyester (Polyethylene Terephthalate – PET):
- Properties: Strong, flexible, transparent, and resistant to tearing or deformation.
- Advantages: The material’s flexibility makes it easy to handle, while its durability allows it to withstand multiple uses without deteriorating. The transparency of polyester also ensures that the emulsion can be viewed clearly without interference from the base.
- Thickness: The typical thickness of the base is around 150-200 microns, designed to ensure optimal handling while maintaining stiffness for image precision.
Functions of the Base Layer:
- Support: Provides a stable structure for the emulsion to be coated on.
- Dimensional Stability: Ensures that the film does not stretch or shrink during handling or processing, maintaining the accuracy of the images.
- Transparency: Allows light and X-rays to pass through with minimal distortion, facilitating clear image reproduction.
2. Emulsion Layer
The emulsion layer is the most critical part of the X-ray film. It contains the light-sensitive material that interacts with X-rays to create the image. The composition of the emulsion determines the film’s sensitivity, contrast, and resolution.
Materials in the Emulsion Layer:
- Silver Halide Crystals (AgBr, AgCl, AgI):
- Composition: The emulsion is primarily composed of silver bromide (AgBr), silver chloride (AgCl), or a combination of these, suspended in gelatin.
- Function: These crystals are sensitive to both visible light and X-rays. When exposed to X-rays, the crystals undergo a chemical change, which forms the latent image that is later developed into a visible one.
- Grain Size: The size of the silver halide crystals affects the film’s sensitivity and resolution. Larger grains increase sensitivity but reduce image sharpness, while smaller grains improve sharpness but require longer exposure times.
- Gelatin:
- Function: Gelatin acts as the binding agent for the silver halide crystals. It holds the crystals evenly dispersed across the film and allows them to interact with light or X-rays.
- Properties: It is transparent and chemically inert, ensuring that it doesn’t interfere with image formation. Gelatin also swells during processing, allowing developer chemicals to penetrate and form the image efficiently.
Key Features of the Emulsion Layer:
- Sensitivity: The film’s ability to respond to X-rays or light is largely determined by the concentration and size of the silver halide crystals.
- Contrast: The emulsion’s contrast depends on how the silver halide crystals react to varying intensities of X-rays. High-contrast films respond to subtle differences in X-ray exposure, making them ideal for diagnostic purposes.
- Resolution: The sharpness of the image is influenced by the uniformity of the emulsion layer and the size of the silver halide grains. Smaller grains offer higher resolution, which is important for detailed medical imaging.
3. Protective Overcoat
In addition to the base and emulsion layers, X-ray film often includes a protective overcoat on both sides to protect the emulsion from physical damage, such as scratches, fingerprints, and dust. This layer is typically made from a transparent polymer.
Function:
- Protection: Shields the sensitive emulsion layer from handling damage and environmental exposure.
- Durability: Enhances the film’s ability to withstand repeated use and processing in medical environments.
4. Anti-Halation Layer
Some X-ray films also include an anti-halation layer. This layer is positioned beneath the emulsion and prevents the reflection of light back through the emulsion, which could cause image blurring or loss of detail.
Material:
- This layer is typically a dye that absorbs light or radiation, ensuring that once the light passes through the emulsion, it does not reflect back.
5. Adhesive Layer
An adhesive layer is often present between the base and emulsion layers to ensure proper bonding and prevent the emulsion from separating during handling or processing.
Material:
- Typically composed of a polymer-based adhesive that bonds the emulsion securely to the base layer without affecting transparency or flexibility.
Summary of X-ray Film Composition:
- Base Layer: Polyester (provides support and transparency).
- Emulsion Layer: Silver halide crystals in gelatin (responsible for image formation).
- Protective Overcoat: Transparent polymer (protects the emulsion).
- Anti-Halation Layer: Light-absorbing dye (prevents image blurring).
- Adhesive Layer: Polymer adhesive (bonds the emulsion to the base).
Understanding the materials used in X-ray film is crucial for selecting the right type of film for specific medical applications, maintaining proper storage conditions, and optimizing image quality. Each component plays a key role in ensuring that the film can accurately capture and reproduce diagnostic images with clarity and detail.
Manufacturing Process of Medical X-Ray Films
1. Raw Material Selection
Base Material
The foundation of an X-ray film is its base material, usually made from polyester. Polyester is chosen for its flexibility, strength, and durability. It needs to be thin enough to allow light to pass through it during the imaging process but strong enough to withstand handling and processing.
Emulsion Layer
The emulsion layer is one of the most important parts of the X-ray film. This layer contains silver halide crystals suspended in gelatin, which are responsible for capturing the X-ray image. The quality and purity of the silver halide used in this layer directly affect the film’s sensitivity and clarity.
2. Coating the Film Base
Once the raw materials are selected, the next step is to coat the film base with the emulsion layer. This process must be done with extreme precision to ensure the thickness of the emulsion is consistent across the entire film. Uneven coating can result in variations in the image quality, making it difficult to obtain accurate diagnostic images.
Applying the Emulsion
The emulsion is applied in a controlled environment to prevent contamination from dust or other particles. The coating process uses advanced machinery to ensure that the emulsion spreads evenly over the surface of the film base.
Drying the Film
After the emulsion is applied, the film must be dried in a carefully controlled environment. Too much heat or humidity can affect the integrity of the film, leading to defects or poor image quality. The drying process is typically done in a cleanroom setting to ensure that the film remains free from contaminants.
3. Sensitizing the Film
Once the film base is coated with the emulsion, the next step is to sensitize the film. This process involves treating the silver halide crystals in the emulsion layer to increase their sensitivity to X-rays. The more sensitive the crystals are, the clearer and sharper the resulting image will be.
Controlling Sensitivity Levels
The sensitizing process must be carefully controlled to ensure that the film is neither too sensitive nor too insensitive. If the film is too sensitive, it can result in overly dark images, making it difficult to see fine details. If it is not sensitive enough, the images may be too faint or lack clarity.
4. Quality Control Testing
Before the films are packaged and distributed, they go through a series of quality control tests to ensure they meet industry standards. Quality control is an essential part of the manufacturing process, as it helps to identify any defects or inconsistencies in the film before it reaches healthcare providers.
Testing for Consistency
The first step in quality control is testing the consistency of the film’s coating and emulsion layer. This ensures that the film will produce uniform images when exposed to X-rays. Any variation in thickness or composition could result in poor-quality images, affecting the accuracy of diagnostic tests.
Sensitivity and Contrast Testing
Next, the film is tested for sensitivity and contrast. These tests help to ensure that the film will respond correctly to varying levels of radiation and produce images with the right amount of contrast. Too much contrast can make it hard to distinguish between different tissues, while too little can result in blurry or faint images.
Durability Testing
Medical X-ray films must also be durable enough to withstand handling, transportation, and processing. Durability tests involve exposing the film to different environmental conditions, such as heat, humidity, and light, to ensure that it maintains its quality under a variety of conditions.
5. Cutting and Packaging
Once the quality control tests are complete, the X-ray films are cut to the appropriate size and packaged for distribution. Proper packaging is essential to protect the films from light exposure and physical damage during shipping and storage.
Cutting the Films
X-ray films are produced in large sheets and then cut to size depending on their intended use. The cutting process must be precise to ensure that the films fit the X-ray machines and processing equipment used by healthcare providers.
Lightproof Packaging
Since X-ray films are sensitive to light, they must be packaged in lightproof materials to prevent exposure before they are used. The packaging is also designed to protect the films from physical damage, such as bending or tearing, during transportation.
6. Environmental Considerations in Manufacturing
Manufacturing X-ray films requires the use of various chemicals and materials, some of which can be harmful to the environment. To minimize their environmental impact, manufacturers must follow strict guidelines for the disposal of waste and the recycling of materials.
Reducing Chemical Waste
The production of X-ray films involves the use of chemicals such as silver and gelatin, which can be harmful if not handled properly. Manufacturers are required to use environmentally friendly practices, such as recycling silver and reducing the amount of chemical waste produced during the manufacturing process.
Energy Efficiency
Another way manufacturers are working to minimize their environmental impact is by improving the energy efficiency of their production processes. By using energy-efficient machinery and reducing water consumption, manufacturers can reduce their carbon footprint and contribute to more sustainable practices.
Practical Tips on Selecting High-Quality X-ray Films
When selecting high-quality X-ray films for specific medical applications, there are several factors to consider to ensure the best performance and diagnostic accuracy. Here are practical tips to help guide the selection process:
1. Match Film Sensitivity to Diagnostic Needs
- High-speed films: Best suited for situations where lower radiation doses are required, such as pediatric imaging or routine diagnostics. These films provide a faster response to X-ray exposure but may slightly compromise image detail.
- Medium-speed films: Offer a balance between image detail and radiation exposure, making them suitable for general radiography applications like chest X-rays.
- Slow-speed films: Deliver high-resolution images with finer detail and are ideal for imaging small structures like extremities, dental applications, or mammography, though they require higher radiation doses.
2. Select the Appropriate Film Type for the Procedure
- Screen films: Designed for use with intensifying screens to reduce radiation exposure. These are commonly used in chest, bone, and abdominal X-rays.
- Non-screen films: Used where extremely fine detail is required, such as in dental or mammographic imaging, though they necessitate higher radiation doses due to the absence of an intensifying screen.
- Dental films: Specially formulated for intraoral and extraoral radiography, available in different sizes and sensitivities tailored to capturing detailed images of teeth and surrounding structures.
3. Consider the Film’s Contrast Characteristics
- High-contrast films: Provide greater differentiation between different tissue densities, making them ideal for detecting subtle changes, such as in bone fractures or soft tissue abnormalities. Use these for applications where clear distinction between shades is critical, such as chest imaging for lung conditions.
- Low-contrast films: Offer more gradual tone variations, which can be useful for imaging areas where fine detail is not as critical, like abdominal radiography.
4. Ensure Compatibility with Imaging Equipment
- Choose films that are compatible with your facility’s X-ray equipment and processing systems (manual or automatic). Consider whether the films are intended for use with film-screen systems, digital radiography, or specific types of processors.
- If your facility uses intensifying screens, make sure the film is properly matched to the screen’s sensitivity and speed. Using incompatible films can result in poor image quality or wasted exposures.
5. Check Film Packaging and Size Options
- Select films that come in sizes appropriate for the specific exam. Common sizes for general radiography include 8×10, 10×12, and 14×17 inches, while smaller films are used for dental or extremity imaging.
- Ensure the packaging offers light protection and the film is sealed properly to prevent exposure before use. Consider individual wrapping for sensitive applications, such as intraoral dental films.
6. Evaluate the Brand and Manufacturing Standards
- Opt for films from reputable manufacturers that comply with ISO standards for medical imaging films. Leading brands typically provide consistent performance, reliable quality, and adhere to international safety and performance guidelines.
- Look for films that have undergone quality assurance testing during production, ensuring uniform coating and sensitivity.
7. Consider Environmental and Storage Conditions
- Choose films that are stable under your facility’s storage conditions. Some films are more sensitive to temperature and humidity changes, so if your storage area is not tightly controlled, it’s best to choose films that tolerate moderate environmental fluctuations.
- Ensure that your facility’s storage conditions, like temperature (15°C to 24°C) and humidity (30% to 50%), align with the films’ requirements to avoid image degradation.
8. Assess Cost and Longevity
- Higher-quality films generally offer better sensitivity, contrast, and diagnostic performance, but they can be more expensive. When selecting a film, consider the cost per film, balancing it against the benefits of improved image quality and reduced re-takes.
- Factor in the potential for bulk purchasing or long-term contracts with suppliers to reduce costs, especially if your facility uses large volumes of X-ray films.
9. Choose Films with Proven Diagnostic Performance
- Seek feedback from other professionals or facilities that have used the specific film for similar procedures. Films that have a proven track record in providing high-quality diagnostic images for specific applications are more likely to meet your needs.
10. Consider Film Sensitometric Properties
- Gamma and Density: Films with a higher gamma (steeper slope) provide better contrast, while those with lower gamma may offer more tonal range. The maximum optical density (D-max) should be adequate to handle the darkest parts of the image without losing detail.
By considering the specific medical applications, film sensitivity, contrast characteristics, equipment compatibility, and environmental factors, healthcare facilities can select the most appropriate X-ray films that deliver high-quality images, improve diagnostic accuracy, and meet the operational demands of their practice.
Impact of X-ray Film Storage and Handling on Image Quality and Shelf Life
Proper storage and handling of X-ray films are crucial for maintaining their image quality and shelf life. Any deviation from recommended practices can lead to significant image degradation, rendering the films useless for diagnostic purposes. Below are key factors that influence the impact of storage and handling on X-ray films:
1. Impact on Image Quality
- Temperature Sensitivity: X-ray films are highly sensitive to temperature fluctuations. Storing them in environments that are either too hot or too cold can cause chemical changes in the emulsion layer. Ideal storage temperatures are typically between 15°C to 24°C (59°F to 75°F). Higher temperatures can lead to premature development of the film, creating fogging or distortion in the image, while lower temperatures can reduce film sensitivity.
- Humidity Control: Humidity levels must be kept within 30% to 50% relative humidity. High humidity can cause the film to stick to the packaging or itself, resulting in artifacts on the image. Low humidity, on the other hand, increases the risk of static artifacts, which show up as unwanted streaks or patterns on the X-ray image. Both high and low humidity can compromise diagnostic quality.
- Light Exposure: Exposure to light can cause irreversible damage to the film, leading to overexposure or fogging. X-ray films are particularly sensitive to white light and must always be stored in light-tight containers or dark environments to prevent accidental exposure. Even brief exposure to light before development can degrade image quality.
2. Effects on Shelf Life
- Expiration Dates: X-ray films have a shelf life indicated by the manufacturer, after which they may lose sensitivity and image quality. Aging can cause the emulsion layer to become less responsive, resulting in underexposed or low-contrast images. To maximize shelf life, always rotate stock and use older films first, while ensuring newer ones are stored properly.
- Chemical Deterioration: Over time, especially under poor storage conditions, the chemicals in the emulsion layer may start to deteriorate, causing image fading or a loss of contrast. Proper storage can significantly extend the film’s useful life beyond the expiration date.
3. Handling Issues
- Physical Damage: Rough handling of X-ray films can cause scratches, creases, or dents, all of which result in permanent artifacts on the image. Mishandling during loading or processing can also lead to dust or debris becoming embedded in the film, which will show up as dark spots on the image.
- Electrostatic Discharge (ESD): Handling films in low-humidity environments increases the risk of static discharge, which appears as branching, lightning-like patterns on the film. This can be mitigated by maintaining appropriate humidity levels and grounding film processors.
- Contamination: Oils from the skin, dirt, or other contaminants can damage the emulsion layer when the film is handled improperly. It’s essential to always handle films by the edges and avoid touching the emulsion surface to prevent contamination.
4. Packaging and Protection
- Secure Packaging: Films should be kept in original packaging until use. The packaging protects them from light exposure, physical damage, and environmental conditions like humidity and dust. Once the original packaging is opened, the films should be stored in lightproof storage boxes or dark rooms.
- Accurate Labeling: Proper labeling of stored X-ray films is essential for avoiding mishandling or misplacement. Accurately labeling film packaging with details such as expiration date, type of film, and date of acquisition ensures that staff can quickly identify and use films before they expire, reducing waste and ensuring quality images.
5. Practical Tips for Storage and Handling
- Avoid Temperature Extremes: Store films in temperature-controlled environments to avoid exposure to extreme heat or cold. Never store films near heat sources like radiators or in locations exposed to direct sunlight.
- Humidity Control: Utilize dehumidifiers or humidifiers to maintain appropriate humidity levels in the storage area. Monitor levels regularly with a hygrometer.
- Proper Positioning: Store films vertically in a dark, clean, and dry environment to prevent bending or warping. Laying them flat can cause pressure-related damage, especially in bulk storage situations.
- Monitor Shelf Life: Implement a first-in, first-out (FIFO) system to use older films before newer ones, reducing the chances of using expired films.
By adhering to proper storage and handling practices, medical facilities can preserve the diagnostic quality of X-ray films, extend their shelf life, and reduce the risks of image degradation, ensuring that the films remain effective tools for accurate medical diagnosis.
Conclusion: Beyond Just Manufacturing
The manufacturing process of medical X-ray films is complex and requires strict attention to detail at every stage. From selecting high-quality raw materials to ensuring that the films meet industry standards through rigorous testing, every step is crucial to producing reliable, high-quality films. Proper manufacturing practices not only ensure that the films produce clear, accurate images but also help to protect the environment through sustainable practices.
By understanding the importance of each step in the process, healthcare providers can feel confident that they are using high-quality X-ray films that meet the highest standards of safety and performance.